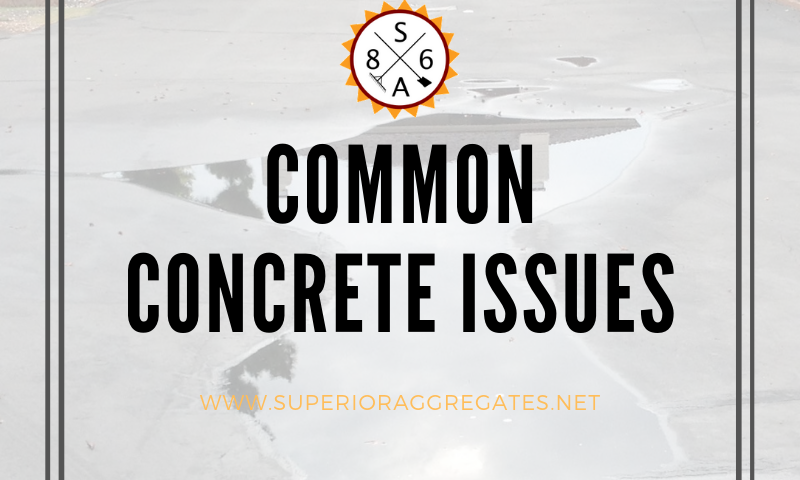
Common Concrete Issues
Concrete is a common material used due to its durability and versatility. Under the right conditions, it is a sustainable material. But, there are numerous common concrete problems, which can prevent concrete from attaining its longevity. Recognizing these problems and understanding the solutions can improve the overall performance of concrete. The common concrete problems include dusting, blistering, plastic shrinkage cracking, discoloration, and scaling.
Dusting
Dusting on concrete occurs when a hardened concrete surface appears as a powdery material. Laitance, which is a layer of cement, water, and fine aggregates is the primary reason why dusting occurs on concrete. The laitance layer is weak, porous, and thin. As a result, the laitance makes the hardened concrete surface vulnerable and weak.
Other reasons why dusting appears include improper cure of the concrete surface, exposing the concrete to carbon dioxide while it is in a plastic state, and conducting finish operation on the concrete surface while it still has bleed water—this is water that separates itself from the concrete.
To avoid these problems, proper concrete curing procedures should always be followed; equipment that produces carbon dioxide should always be vented while the surface is in the plastic state, and the finishing operation should always be conducted on the concrete surface after bleed water has been removed.
Blistering
Blistering appears on a hardened or fresh concrete surface as bumps. These blisters occur when bleeding water or entrapped air rises to the sealed concrete surface. Blistering of concrete surfaces is problematic, as it causes the concrete to break easily under stresses like traffic. Other reasons why blistering occurs include excessive or inadequate use of vibration during concrete compaction, setting concrete surfaces over the vapor barrier, and sealing the concrete surface early.
To prevent blistering from occurring, appropriate concrete compaction procedures have to be followed, if possible, concrete should not be placed over vapor barriers, and trowel blades must be kept flat at all times to avoid sealing the concrete surface early.
Plastic Shrinkage Cracking
Plastic shrinkage cracking occurs when a crack appears on fresh, hardened concrete surfaces. Like the name suggests, these cracks develop while the surface is still in the plastic state. These cracks occur when the concrete surface experiences a rapid loss of water before it sets. Although plastic shrinkage cracking is an aesthetics issue and not a structural issue, these cracks end up allowing chemicals to penetrate the surface, and this can result in structural problems later on.
The loss of water on concrete surfaces can occur due to several reasons like low relative humidity, high winds, and high concrete temperature or ambient air. To avoid these conditions, ensure you use fog spraying equipment, windscreens and windbreaks should be installed, and always avoid placing concrete at midday.
Discoloration
Discoloration of concrete can occur due to various reasons like material exposure, weather conditions, and even the curing time. Although concrete discoloration may look aesthetically unpleasing, there are numerous ways you can repair these issues. The first method is using a concrete cleaner. These will help give the concrete a better and natural look. If that does not work, you consider using a concrete stain.
Scaling
Scaling on concrete surfaces occurs when the surfaces start to chip or flake away. This is usually because of freeze-thaw, water seepage, poor concrete finishing, or weak concrete surfaces. To repair scaling issues, use trowel-grade light coat, as it helps fill the scaled area. Also, ensure that you seal your concrete at all times, as this helps to reduce scaling significantly.
Concrete is a common material used due to its durability and versatility. Under the right conditions, it is a sustainable material. But, there are numerous common concrete problems, which can prevent concrete from attaining its longevity. Recognizing these problems and understanding the solutions can improve the overall performance of concrete. The common concrete problems include dusting, blistering, plastic shrinkage cracking, discoloration, and scaling.
Dusting
Dusting on concrete occurs when a hardened concrete surface appears as a powdery material. Laitance, which is a layer of cement, water, and fine aggregates is the primary reason why dusting occurs on concrete. The laitance layer is weak, porous, and thin. As a result, the laitance makes the hardened concrete surface vulnerable and weak.
Other reasons why dusting appears include improper cure of the concrete surface, exposing the concrete to carbon dioxide while it is in a plastic state, and conducting finish operation on the concrete surface while it still has bleed water—this is water that separates itself from the concrete.
To avoid these problems, proper concrete curing procedures should always be followed; equipment that produces carbon dioxide should always be vented while the surface is in the plastic state, and the finishing operation should always be conducted on the concrete surface after bleed water has been removed.
Blistering
Blistering appears on a hardened or fresh concrete surface as bumps. These blisters occur when bleeding water or entrapped air rises to the sealed concrete surface. Blistering of concrete surfaces is problematic, as it causes the concrete to break easily under stresses like traffic. Other reasons why blistering occurs include excessive or inadequate use of vibration during concrete compaction, setting concrete surfaces over the vapor barrier, and sealing the concrete surface early.
To prevent blistering from occurring, appropriate concrete compaction procedures have to be followed, if possible, concrete should not be placed over vapor barriers, and trowel blades must be kept flat at all times to avoid sealing the concrete surface early.
Plastic Shrinkage Cracking
Plastic shrinkage cracking occurs when a crack appears on fresh, hardened concrete surfaces. Like the name suggests, these cracks develop while the surface is still in the plastic state. These cracks occur when the concrete surface experiences a rapid loss of water before it sets. Although plastic shrinkage cracking is an aesthetics issue and not a structural issue, these cracks end up allowing chemicals to penetrate the surface, and this can result in structural problems later on.
The loss of water on concrete surfaces can occur due to several reasons like low relative humidity, high winds, and high concrete temperature or ambient air. To avoid these conditions, ensure you use fog spraying equipment, windscreens and windbreaks should be installed, and always avoid placing concrete at midday.
Discoloration
Discoloration of concrete can occur due to various reasons like material exposure, weather conditions, and even the curing time. Although concrete discoloration may look aesthetically unpleasing, there are numerous ways you can repair these issues. The first method is using a concrete cleaner. These will help give the concrete a better and natural look. If that does not work, you consider using a concrete stain.
Scaling
Scaling on concrete surfaces occurs when the surfaces start to chip or flake away. This is usually because of freeze-thaw, water seepage, poor concrete finishing, or weak concrete surfaces. To repair scaling issues, use trowel-grade light coat, as it helps fill the scaled area. Also, ensure that you seal your concrete at all times, as this helps to reduce scaling significantly.