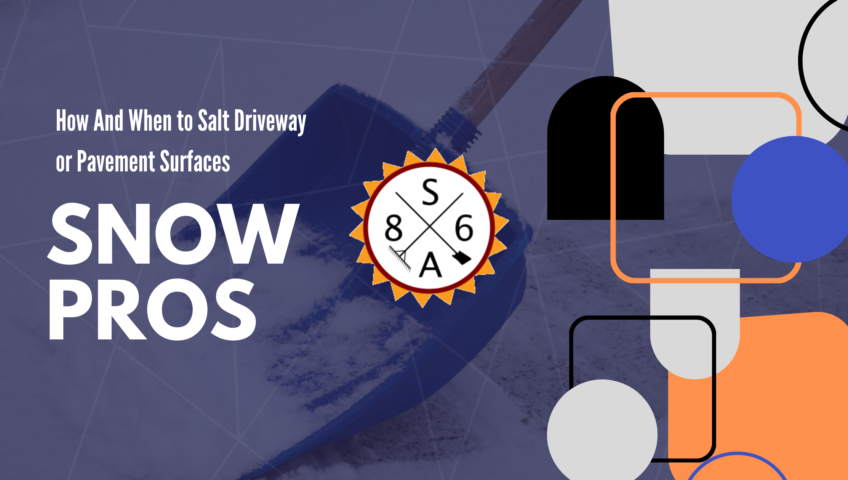
How And When to Salt Driveway or Pavement Surfaces | Snow Removal Pros
Winter is upon us once again, which can only mean one thing – much of the country will soon be bombarded by a plethora of winter storms, if that isn’t already the case.
If you live in a part of the country that experiences all four seasons, you’re no doubt familiar with the trucks that drive around neighborhoods that salt the roadways to keep things safe. Of course, this demands the question – when should you salt your driveway or pavement surfaces, and how do you best go about accomplishing that goal? The answers to questions like those require you to keep a few key things in mind.
Show Removal Basics: Breaking Things Down
One of the most important things to understand about this process in general is that you’ll need to take a very proactive approach when it comes to snow removal.
That is to say, you shouldn’t wait for the snow to fall before you begin taking care of the situation. In a best case scenario, you should put salt down on places like your driveway asphalt and other surfaces prior to the beginning of the storm. Spread salt evenly across your surfaces to make sure that you have equal protection moving forward.
Even if a storm cropped up unexpectedly and snow is already on the ground, don’t worry – you can still put salt down. Yes, it’s true that the poor weather will likely make it more difficult to do so. But especially as the storm drags on, this is very much one of those situations where doing something is better than doing nothing at all.
Especially if you’re dealing with asphalt surfaces, you should be judicious about where you put down salt. While it’s true that products like rock salt can cause long-term damage to concrete, they aren’t nearly as hard on the asphalt itself. This is because asphalt is less porous than concrete is. Because of that, it will hold up better to the application of salt over the long-term. This is also part of the reason why, if you’re thinking about having something like your driveway redone, and you live in an area of the country that experiences significant winter storms, asphalt would certainly be an option that you would want to consider.
Beyond that, knowing how and when to salt your driveway or pavement surfaces requires you to come to a better understanding of how salt actually works in this context. Most of the products that you’re likely to find in a local hardware or home improvement store work by lowering the freezing point of water. This makes it more difficult for ice to form over longer periods of time. This is also a big part of the reason why it’s so important to put salt down prior to any upcoming winter weather – you’re not trying to solve a problem, you’re trying to prevent one from happening at all.
If you are dealing with concrete surfaces, there are other environmentally friendly products that you can consider. They’re less harsh on the concrete than rock salt, although you may not see the results quite as quickly. Likewise, you may have to put more of the product down on the ground than you would with rock salt – although when you consider that you’re preventing damage to your surfaces, that may be worth what many perceive to be a minor inconvenience.
If you’d like to find out more information about how and when to salt driveway or pavement surfaces on or around your property, or if you’d just like to speak to experts at local concrete companies in a bit more detail, please don’t delay – contact us today.
Winter is upon us once again, which can only mean one thing – much of the country will soon be bombarded by a plethora of winter storms, if that isn’t already the case.
If you live in a part of the country that experiences all four seasons, you’re no doubt familiar with the trucks that drive around neighborhoods that salt the roadways to keep things safe. Of course, this demands the question – when should you salt your driveway or pavement surfaces, and how do you best go about accomplishing that goal? The answers to questions like those require you to keep a few key things in mind.
Show Removal Basics: Breaking Things Down
One of the most important things to understand about this process in general is that you’ll need to take a very proactive approach when it comes to snow removal.
That is to say, you shouldn’t wait for the snow to fall before you begin taking care of the situation. In a best case scenario, you should put salt down on places like your driveway asphalt and other surfaces prior to the beginning of the storm. Spread salt evenly across your surfaces to make sure that you have equal protection moving forward.
Even if a storm cropped up unexpectedly and snow is already on the ground, don’t worry – you can still put salt down. Yes, it’s true that the poor weather will likely make it more difficult to do so. But especially as the storm drags on, this is very much one of those situations where doing something is better than doing nothing at all.
Especially if you’re dealing with asphalt surfaces, you should be judicious about where you put down salt. While it’s true that products like rock salt can cause long-term damage to concrete, they aren’t nearly as hard on the asphalt itself. This is because asphalt is less porous than concrete is. Because of that, it will hold up better to the application of salt over the long-term. This is also part of the reason why, if you’re thinking about having something like your driveway redone, and you live in an area of the country that experiences significant winter storms, asphalt would certainly be an option that you would want to consider.
Beyond that, knowing how and when to salt your driveway or pavement surfaces requires you to come to a better understanding of how salt actually works in this context. Most of the products that you’re likely to find in a local hardware or home improvement store work by lowering the freezing point of water. This makes it more difficult for ice to form over longer periods of time. This is also a big part of the reason why it’s so important to put salt down prior to any upcoming winter weather – you’re not trying to solve a problem, you’re trying to prevent one from happening at all.
If you are dealing with concrete surfaces, there are other environmentally friendly products that you can consider. They’re less harsh on the concrete than rock salt, although you may not see the results quite as quickly. Likewise, you may have to put more of the product down on the ground than you would with rock salt – although when you consider that you’re preventing damage to your surfaces, that may be worth what many perceive to be a minor inconvenience.
If you’d like to find out more information about how and when to salt driveway or pavement surfaces on or around your property, or if you’d just like to speak to experts at local concrete companies in a bit more detail, please don’t delay – contact us today.